Using Different Angles of Rotating Blades Using the Finite Element Method
DOI:
https://doi.org/10.51173/jt.v6i2.1673Keywords:
Design, Rotator, Biomimetic, Finite ElementAbstract
One of the most important operations in agriculture is tillage, which has a great contribution to increasing crop yield and aeration of the soil and, ultimately, root development. Among the important tools for tillage are rotary rotators that are exposed to high and variable dynamic loads, so they are designed to have both the greatest contribution to soil agitation and high strength; It is necessary. Therefore, in this research, an L-shaped blade sample was designed for a rotator using a Biomimetic method. Due to the extensive research that has been done in the world in the field of manufacturing different types of rotators with a rotating agitator mechanism, therefore, it is necessary to study and optimize the rotator blades according to Iranian conditions. In this study, the studied variables include dependent and independent variables. Dependent variables include von Mises stress and arm displacement, and independent variables include the dimensions and geometric parameters of the Shape of the Rotator Blades. The idea for the blade design was inspired by the paw of a mole rat. Six blades were designed by simple method and biomimetic method and then by finite element method. Effects of blade angle change and design method on stress distribution, maximum displacement, maximum energy absorbed in the blade, reliability and under 400 N checked out. The results showed that in all designed models, the values of stress, displacement and energy absorbed were lower in the biomimetic design mode. As the blade angle increased, the values of the above parameters also decreased. Finally, the best model for having the least von Mises stress and the highest reliability was the blade with a Biomimetic design and a 20-degree angle.
Downloads
References
L. Zhang, P. Jia, T. Huang, and B. Wang, “Optimal design method for composite blades using stiffness weights”, J.Composite Structures , vol.238,pp.111880,2020, https://doi.org/10.1016/j.compstruct.2020.111880.
H. Zhang, H. Yuan, and H. Sun, “Vibration reduction optimization for mistuned bladed disk based on reduced order modeling technique”, Journal of Vibroengineering, vol. 23, no. 2, pp. 385–399, Dec. 2020, doi: 10.21595/jve.2020.21381.
B. Tandale, Saurabh, B. Markert, and M. Stoffel,” Intelligent stiffness computation for plate and beam structures by neural network enhanced finite element analysis”, International Journal for Numerical Methods in Engineering,vol. 123,no.17 ,pp. 4001-4031,2022, https://doi.org/10.1002/nme.6996.
H.Jiasheng, Kai Wang , Jiabo Tang, Jialu Xu, and H. Song “An experimental study of the centrifugal hardening effect on rotating cantilever beams”, Mechanical Systems and Signal Processing ,vol.165,pp.108291,2022, https://doi.org/10.1016/j.ymssp.2021.108291.
Sumin Cho, D. Lee, Sunmin Jang, Sunghwan Cho, Jaehan Shim, Y. Jang, Zong-Hong Lin, K. Choi, D. Choi. “Physical intelligence-based working mode adaptable triboelectric nanogenerator for effective wind energy harvesting in broad range”, Nano Energy ,vol.113,pp.108608,2023, https://doi.org/10.1016/j.nanoen.2023.108608.
X. Sun, Q. Hu, L. Yan, Ye Chen, K. Zhang, J. Qu “A magnetic torque optimization method for a hydraulic–magnetic coupling-drive cuttings cleaning tool”, Natural Gas Industry B ,vol.6,no.4,pp.374-383,2019, https://doi.org/10.1016/j.ngib.2019.01.013.
C. Yuhn, Y. Sato, H. Kobayashi, A. Kawamoto, T. Nomura “4D topology optimization: Integrated optimization of the structure and self-actuation of soft bodies for dynamic motions”, Computer Methods in Applied Mechanics and Engineering,vol.414, pp.116187,2023, https://doi.org/10.1016/j.cma.2023.116187.
S. Hooman ,” Development of a Finite Element Analysis Workflow for Studying Reverse Total Shoulder Arthroplasty”,2021, http://hdl.handle.net/1828/13032.
L. Jonggeon, P. Jaesung, K.Euiyoung and C. Maenghyo,“Reduced order modeling based on an element-wise stiffness evaluation procedure for photo-responsive polymer structures”, AIAA Scitech ,2019 Forum, https://doi.org/10.2514/6.2019-1023.
Zhiyuan Jiang, Xianzhen Huang, Huizhen Liu, Zhiqun Zheng, Shangjie Li, and Shanshan Du, “ Dynamic reliability analysis of main shaft bearings in wind turbines”, International Journal of Mechanical Sciences,vol. 235, pp.107721,2022, https://doi.org/10.1016/j.ijmecsci.2022.107721.
A. Abbasi, K. Al-Khaled, M. Ijaz Khan, S. Khan, A. El-Refaey, W. Farooq, M. Jameel, S. Qayyum,” Optimized analysis and enhanced thermal efficiency of modified hybrid nanofluid (Al2O3, CuO, Cu) with nonlinear thermal radiation and shape features”, Thermal Engineering journal, vol.28, pp. 101425,2021, https://doi.org/10.1016/j.csite.2021.101425.
J. Zhang, R. Yaoyao, H. Xiangying, Z. Hong, “ Design And Power Generation Performance Analysis of A Rim-Driven Wave Energy Generator”, Research Square journal, 2021, https://doi.org/10.21203/rs.3.rs-746622/v1.
G. d'Alessandro, L. Mele. F. Columbro, G. Amico, S. Marnieros, S. Masi, and A. Mennella. “QUBIC VI: Cryogenic half wave plate rotator, design and performance”, Journal of Cosmology and Astroparticle Physics, vol.04, no.39, 2022, DOI 10.1088/1475-7516/2022/04/039.
K. Anna, A. Krahl, A. Lipphaus, P . Sander, and U. Witzel “Determination of muscle strength and function in plesiosaur limbs: finite element structural analyses of Cryptoclidus eurymerus humerus and femur”, PeerJ, vol.10, no.3, pp.13342,2022, DOI: 10.7717/peerj.13342.
C. Ignacio Rivero, Finite Element Modeling of Patient-Specific Total Shoulder Arthroplasty, Diss: University of Denver,2023.
F. Schaardenburgh, H. Magré,K. Willemsen, B.Rietbergen, and S. Nijs, “ Prediction of the Proximal Humerus Morphology Based on a Statistical Shape Model with Two Parameters: Comparison to Contralateral Registration Method”, Bioengineering J, vol.10, no.10, pp. 1185,2023, https://doi.org/10.3390/bioengineering10101185.
T. R. Hoffman, J. D. Lamplot, S. J. McClish, C. Payne, and P. J. Denard, “Three Medial All Suture Anchors Improves Contact Force Compared to Two Hard Body Anchors in a Biomechanical Two-Tendon Rotator Cuff Tear Model”, Arthroscopy, sports medicine, and rehabilitation, J.ASMR, vol. 4, no.5, pp.1601-1607, 5 Aug. 2022.
A. Zhou, J. Shi, Yi Ma, X. Xu, “Improved resonance method for fatigue test of full-scale wind turbine blades”, AIP Advances J, vol.12, no.8, 2022, https://doi.org/10.1063/5.0095283
Igor Petrovic, J. M. Jeknic-Dugic, and M. Arsenijevic” The Role of Size and Shape in the Stability of the Quantum Brownian Rotator”, 11th International Conference of the Balkan Physical Union,2022, DOI: 10.22323/1.427.0173.
H. Menéndez, E. Altshuler, N. Brilliantov. and T. Pöschel, “Lack of collective motion in granular gases of rotators”, New Journal of Physics, vol.24, no.7, pp. 073002,2022, DOI 10.1088/1367-2630/ac78fb.
K. Parveen, S. Sharma, and R. Singh,” Recent trends and future outlooks in manufacturing methods and applications of FGM: a comprehensive review”, Materials and Manufacturing Processes, vol.38, no.9, pp. 1033-1067,2023, https://doi.org/10.1080/10426914.2022.2075892.
Rúnarsson, Sigurður Rúnar. Designing and constructing a prototype standalone bioreactor using 3D printing and finite element analysis: a tool to define osteogenic differentiation in a 3D mechanical environment. Diss. 2019.
T. Pastor, I. Zderic, K. P. van Knegsel, F. Beeres, and S. Nebelung, “Biomechanical analysis of helical versus straight plating of proximal third humeral shaft fractures”, Archives of orthopaedic and trauma surgery J, vol. 143, no.8, pp. 4983-4991,2023, doi:10.1007/s00402-023-04814-0.
M. Cheng,” A summary of acoustic characteristics and control techniques of underwater non-cavitation thruster”, J. Mechanical Engineering Science, vol.233, no.18, pp. 6339-6356,2019, doi:10.1177/0954406219844530.
H.T. Endez, E. Altshuler, N. V. Brilliantov and T. Oschel, “Lack of collective motion in granular gases of rotators”, New Journal of Physics, vol.24, no.7, pp.073002,2021.
J.H. Roberts, O.S. Barnouin, M.G. Daly, K.J. Walsh, and M.C. Nolan “Rotational states and shapes of Ryugu and Bennu: Implications for interior structure and strength”, Planetary and Space Science, vol.204, pp. 105268,2022, https://doi.org/10.1016/j.pss.2021.105268.
K. Rong, H. Ding, and J. Tang, “Data-driven process control for manufacturing spiral bevel and hypoid gears by using design for six sigma (DFSS) considering numerical loaded tooth contact analysis (NLTCA)”, Journal of Engineering Manufacture, vol.235, no.12, pp. 1875-1891,2021, https://doi.org/10.1177/09544054211023625.
I. Petrović, J. Jeknić-Dugić, M. Arsenijević, M. Dugić, and S. Gocić, “The role of size and shape in the stability of the quantum Brownian rotator,” Proc. Sci., vol. 427, Oct. 2023, doi: 10.22323/1.427.0173.
Qian Bing, Yinkang Ran, Qiang Ding, W. Sun and Chenyuan Ma “Experiment and Simulation Analysis of the Vibration Response of the Rotor-bearing System”, Research Squar, 2023, https://doi.org/10.21203/rs.3.rs-1951821/v1.
Gao, Hongbin, Y. Gong, and N. Sun,” An improved concentrated mass method for analysis of the mechanics modes of a four-stage pump rotor system”, Mechanics of Advanced Materials and Structures journal, vol. 28, no.13, pp. 1398-1413,2021, https://doi.org/10.1080/15376494.2021.1922788.
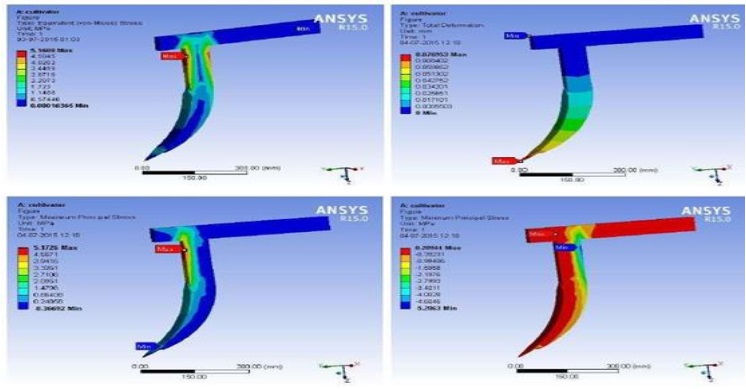
Downloads
Published
How to Cite
Issue
Section
License
Copyright (c) 2024 Hassan Ali Hassan, Ahmad Soheili Mehdizadeh

This work is licensed under a Creative Commons Attribution 4.0 International License.