Enhancing the Tribological Characteristics of Epoxy Composites by the Use of Three-Dimensional Carbon Fibers and Cobalt Oxide Nanowires
DOI:
https://doi.org/10.51173/jt.v6i2.2439Keywords:
Tribological Performance, Epoxy Composites, 3D Carbon Fibers, Cobalt Oxide NanowiresAbstract
In this paper, the results of our research were presented into the sliding wear behaviors of reinforced epoxy composites made with 3D networked carbon fibers ornamented with nanowires of cobalt oxides (NWRs@CFs). Composites are made using the cast-in-place method. Under different normal loads and sliding velocities, these composites' wear and friction coefficient performances are assessed. Tests were performed at 400 rpm spindle speed, 10, 20, and 30 N normal load, and a duration of 300 seconds. Pure epoxy exhibits wear rates of 0.449, 0.481, and 0.501 * 10-5 mm3/Nm at 10, 20, and 30N. Conversely, 3D CFs/epoxy composites exhibit lower wear rates (0.334, 0.360, and 0.390 * 10-5 mm3/Nm) at the same pressure. The epoxy composites of NWRs@CFs wear less, measuring 2.1, 3.5, and 0.4 * 10-5 mm3/Nm under applied loads. The effects of speed on the tribological characteristics were also studied, the friction coefficients for 400, 800, and 600 rpm at 10 N. Pure Epoxy has fraction coefficients of 0.449, 0.494, and 0.552µ at 400, 800, and 600 rpm. In comparison, three-dimensional carbon fibers and epoxy composites show reduced wear rates (0.334, 0.376, and 0.304 µ) under identical loads. Epoxy composites of NWRs@CFs have friction coefficients of 0.261, 0.304, and 0.332µ. Pure epoxy has high wear, indicating less friction resistance.
Downloads
References
X.-J. Shen, X.-Q. Pei, Y. Liu, and S.-Y. Fu, "Tribological performance of carbon nanotube–graphene oxide hybrid/epoxy composites," Composites Part B: Engineering, vol. 57, pp. 120-125, 2014, https://doi.org/10.1016/j.compositesb.2013.09.050.
N. Sharma, S. Kumar, and K. Singh, "Taguchi’s DOE and artificial neural network analysis for the prediction of tribological performance of graphene nano-platelets filled glass fiber reinforced epoxy composites under the dry sliding condition," Tribology International, vol. 172, p. 107580, 2022, https://doi.org/10.1016/j.triboint.2022.107580.
V. Patel, U. Joshi, A. Joshi, B. K. Matanda, K. Chauhan, A. D. Oza, et al., "Multi-Walled Carbon-Nanotube-Reinforced PMMA Nanocomposites: An Experimental Study of Their Friction and Wear Properties," Polymers, vol. 15, p. 2785, 2023, https://doi.org/10.3390/polym15132785.
H. Jagadeesh, P. Banakar, P. Sampathkumaran, R. Sailaja, and J. K. Katiyar, "Influence of nanographene filler on sliding and abrasive wear behaviour of Bi-directional carbon fiber reinforced epoxy composites," Tribology International, vol. 192, p. 109196, 2024, https://doi.org/10.1016/j.triboint.2023.109196.
W. Zhang, X. Shu, S. Cheng, X. Li, T. Hu, and C. Zhang, "Geometry effect of different PTFE fillers on self-lubricating PF composites: Mechanical and tribological properties," Journal of Materials Research and Technology, vol. 28, pp. 22-30, 2024, https://doi.org/10.1016/j.jmrt.2023.11.267.
A. K. Kasar, N. Gupta, P. K. Rohatgi, and P. L. Menezes, "A brief review of fly ash as reinforcement for composites with improved mechanical and tribological properties," Jom, vol. 72, pp. 2340-2351, 2020, https://doi.org/10.1007/s11837-020-04170-z.
A. Pattanaik, M. P. Satpathy, and S. C. Mishra, "Dry sliding wear behavior of epoxy fly ash composite with Taguchi optimization," Engineering Science and Technology, an International Journal, vol. 19, pp. 710-716, 2016, https://doi.org/10.1016/j.jestch.2015.11.010.
M. Z. Hussain, S. Khan, and P. Sarmah, "Effect of dry sliding wear parameters on the specific wear rate of α-MnO2-epoxy nanocomposites," Proceedings of the Institution of Mechanical Engineers, Part C: Journal of Mechanical Engineering Science, vol. 237, pp. 1370-1392, 2023, https://doi.org/10.1177/09544062221132405.
K. Shahapurkar, V. Chenrayan, M. E. M. Soudagar, I. A. Badruddin, P. Shahapurkar, A. Elfasakhany, et al., "Leverage of environmental pollutant crump rubber on the dry sliding wear response of epoxy composites," Polymers, vol. 13, p. 2894, 2021, https://doi.org/10.3390/polym13172894.
C. Gill and J. Sidhu, "Dry Sliding wear behavior of epoxy based composites filled with WS2 and B4C," International Journal of Material Sciences and Technology, vol. 6, pp. 21-32, 2016.
T. Singh, B. Gangil, L. Ranakoti, and A. Joshi, "Effect of silica nanoparticles on physical, mechanical, and wear properties of natural fiber reinforced polymer composites," Polymer Composites, vol. 42, pp. 2396-2407, 2021, https://doi.org/10.1002/pc.25986.
N. A. Ai, S. Hussein, M. Jawad, and I. Al-Ajaj, "Effect of Al2O3 and SiO2 nanopartical on wear, hardness and impact behavior of epoxy composites," Chemistry and materials Research, vol. 7, pp. 34-40, 2015.
A. Nassar, M. Younis, M. Ismail, and E. Nassar, "Improved wear-resistant performance of epoxy resin composites using ceramic particles," Polymers, vol. 14, p. 333, 2022, https://doi.org/10.3390/polym14020333.
T. Albahkali, A. Fouly, I. A. Alnaser, M. B. Elsheniti, A. Rezk, and H. S. Abdo, "Investigation of the Mechanical and Tribological Behavior of Epoxy-Based Hybrid Composite," Polymers, vol. 15, p. 3880, 2023, https://doi.org/10.3390/polym15193880.
A. S. Thakur, N. Sharma, S. Kango, and S. Sharma, "Effect of nanoparticles on epoxy based composites: A short review," Materials Today: Proceedings, vol. 44, pp. 4640-4642, 2021, https://doi.org/10.1016/j.matpr.2020.10.924.
N. Kadhim, A. Zaman, M. Jiang, X. Yang, J. Qiu, and Z. Zhou, "A cast-in-place fabrication of high performance epoxy composites cured in an in-situ synthesized 3D foam of nanofibers," Composites Part B: Engineering, vol. 205, p. 108495, 2021, https://doi.org/10.1016/j.compositesb.2020.108495.
N. Kadhim, Y. Mei, Y. Wang, Y. Li, F. Meng, M. Jiang, et al., "Remarkable improvement in the mechanical properties of epoxy composites achieved by a small amount of modified helical carbon nanotubes," Polymers, vol. 10, p. 1103, 2018, https://doi.org/10.3390/polym10101103.
Y. Xu, Y. Zhang, L. Cheng, L. Zhang, J. Lou, and J. Zhang, "Preparation and friction behavior of carbon fiber reinforced silicon carbide matrix composites," Ceramics international, vol. 33, pp. 439-445, 2007, https://doi.org/10.1016/j.ceramint.2005.10.008.
N. K. Taieh, S. K. Khudhur, E. A. A. Fahad, Z. Zhou, and D. Hui, "High mechanical performance of 3-aminopropyl triethoxy silane/epoxy cured in a sandwich construction of 3D carbon felts foam and woven basalt fibers," Nanotechnology Reviews, vol. 12, p. 20220519, 2023, https://doi.org/10.1515/ntrev-2022-0519.
N. K. Taieh, "A Study of the Chemical Resistance and Hardness of Epoxy Reinforced by Magnesium oxide and charcoal l activated Particles.", Eng. &Tech.Journal, Vol.34, Part (A), No.5, 2016.
Y. Li, W. Wei, Y. Wang, N. Kadhim, Y. Mei, and Z. Zhou, "Construction of highly aligned graphene-based aerogels and their epoxy composites towards high thermal conductivity," Journal of Materials Chemistry C, vol. 7, pp. 11783-11789, 2019, https://doi.org/10.1039/C9TC02937K.
Y. Du, Z. Zhang, D. Wang, L. Zhang, J. Cui, Y. Chen, et al., "Enhanced tribological properties of aligned graphene-epoxy composites," Friction, vol. 10, pp. 854-865, 2022, https://doi.org/10.1007/s40544-021-0496-2.
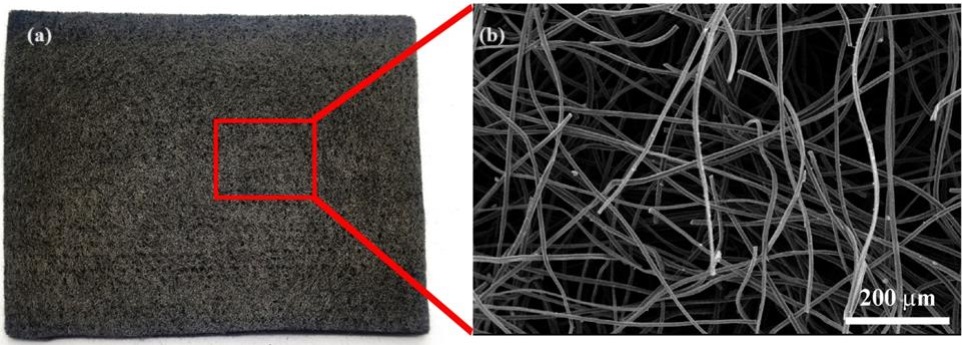
Downloads
Published
How to Cite
Issue
Section
License
Copyright (c) 2024 Muad Muhammed Ali, Haidar Akram Hussein, Nabil Kadhim Taieh, Ying Li, Riad Abdul Abas, Sumair Ahmed Soomro, Salman Aatif

This work is licensed under a Creative Commons Attribution 4.0 International License.